What is Passivation?
Passivation is a chemical process in which the surface of a material is coated in such a way that it becomes “passive,” or less easily corroded by the environment. For example: Painting a wood door so that it is more durable to the elements could be considered a crude form of passivation.
When exposed to air, many metals form a passivation layer via oxidation. But many metals are materially damaged by their environment, usually by some sort of corrosion in the form of rust. In other instances, fabrication processes can introduce surface contaminants that will damage the metal’s integrity over time and hinder its ability to withstand corrosion. By subjecting the metal to a passivation process, the surface layer is artificially applied and strengthened, giving it improved resistance to corrosion without changing the outward appearance of the base material.
How does Passivation Work?
Our passivation process involves immersing stainless steel parts in a nitric or citric acid bath. This removes free iron from the surface of the stainless steel. When the stainless steel is exposed to oxygen-containing environments, a thin chromium oxide film layer is then formed which makes the material more resistant to corrosion due to the lack of iron particles on the surface of the material.
While most stainless steels naturally form this protective oxide layer, the passivation process thickens the layer and significantly speeds up the process. The oxide layer creates a passive surface that acts as protection from corrosive environmental stimuli.
Unlike electropolishing, passivation:
- Does not dissolve the outer layer of the material
- Does not use electricity as part of the process
- Does not change the appearance of the material
The 300 series stainless steel alloys are best suited for passivation. However, some of the 400 and other high sulfide series alloys are not the best candidates for the passivation process. For assemblies that will need to be passivated, all components should be made of the same alloy to retain a consistent appearance.
With over 20 years of experience and a commitment to quality standards and processes, Electro-Max, Inc. provides the best service, unsurpassed quality, and superior passivation services. EMI is NADCAP accredited, fully registered to ISO9001:2015, and complies with ASTM A380, ASTM A 967, AMS 2700, QQ-P-35, SPS-1001, PS 2026, or customer-specific standards.
Contact us today to learn more.
Electro-Max, Inc. is your go-to for all electropolishing services in a variety of industries! Certain industries need high levels of durability and corrosion resistance in their finished parts. Turn to Electro-Max, Inc. for first-class electropolishing and passivation services.
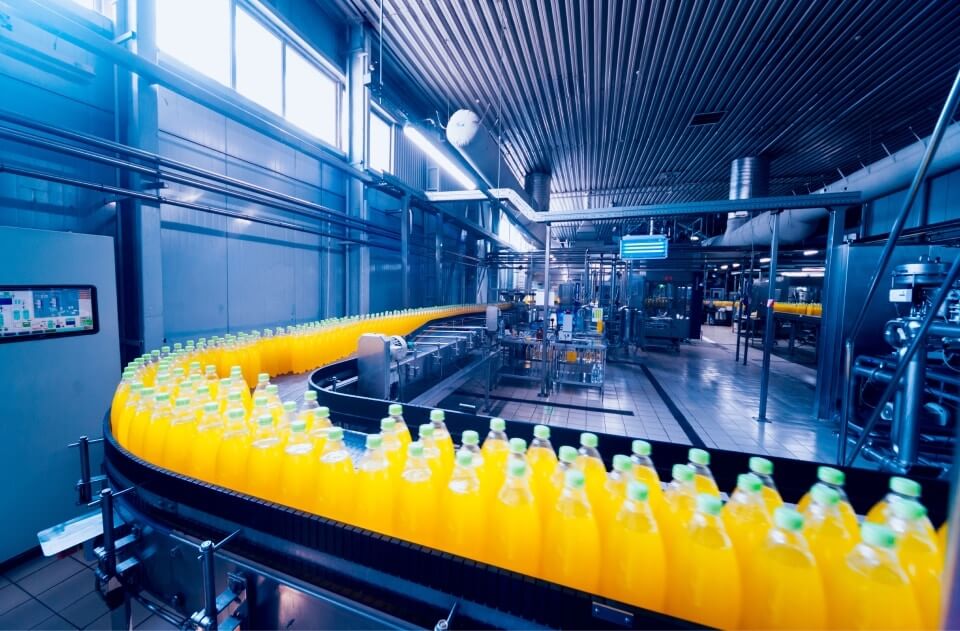
Food & Beverage
Don’t put your equipment at risk! Electropolishing and passivation services from Electro-Max are proven solutions for improving the corrosion resistance of food-grade metal parts.
Learn More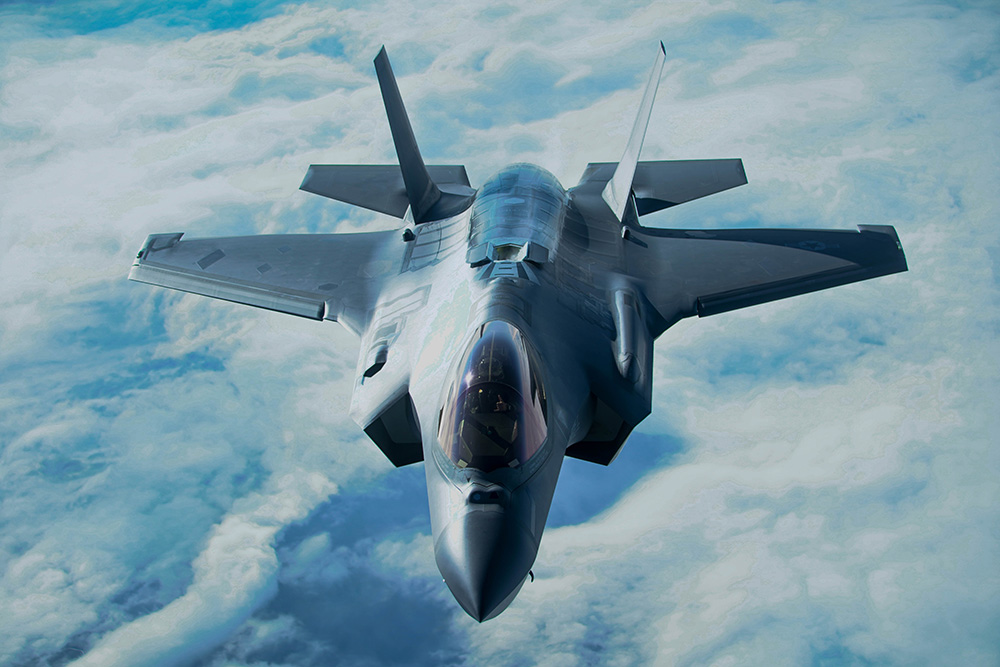
Aerospace & Defense
Aerospace has some of the most stringent requirements of any industry with respect to the structural integrity of metal parts.
Learn More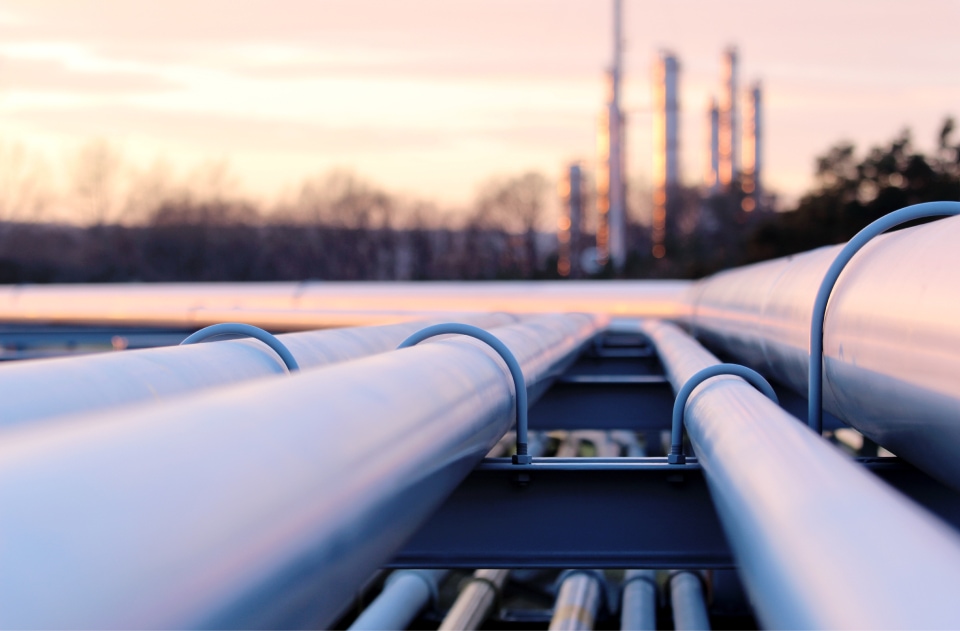
Oil & Gas
By utilizing electropolishing services for stainless steel components, the oil and gas industry can benefit from improved corrosion resistance, efficient cleanability, enhanced surface cleanliness, visual inspection capabilities, and more.
Learn More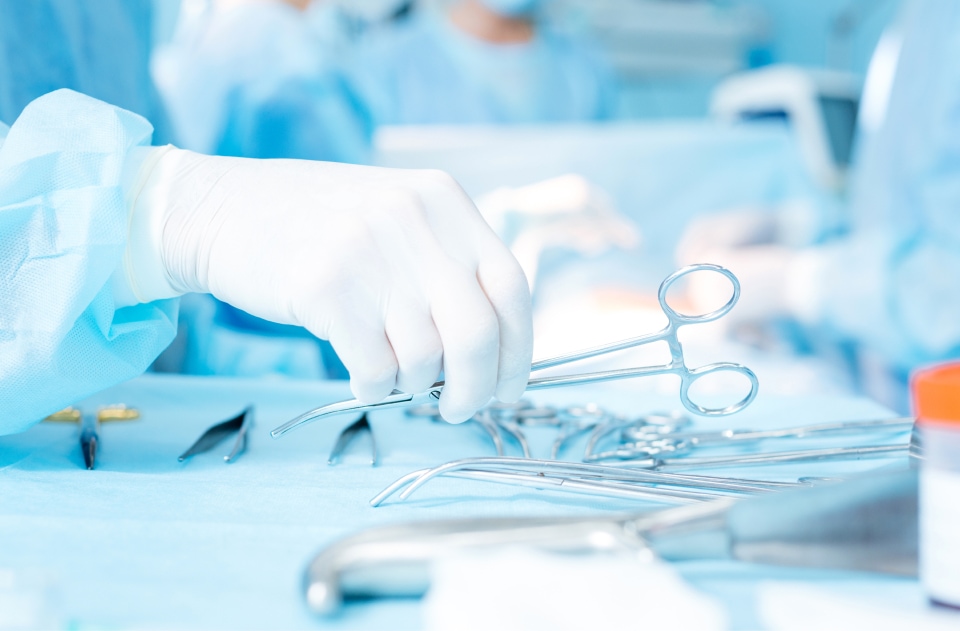
Medical
In the ever-evolving landscape of medical technology, precision, cleanliness, and longevity are paramount. Electro-Max, Inc. stands at the forefront, offering specialized medical electropolishing services and medical passivation services.
Learn More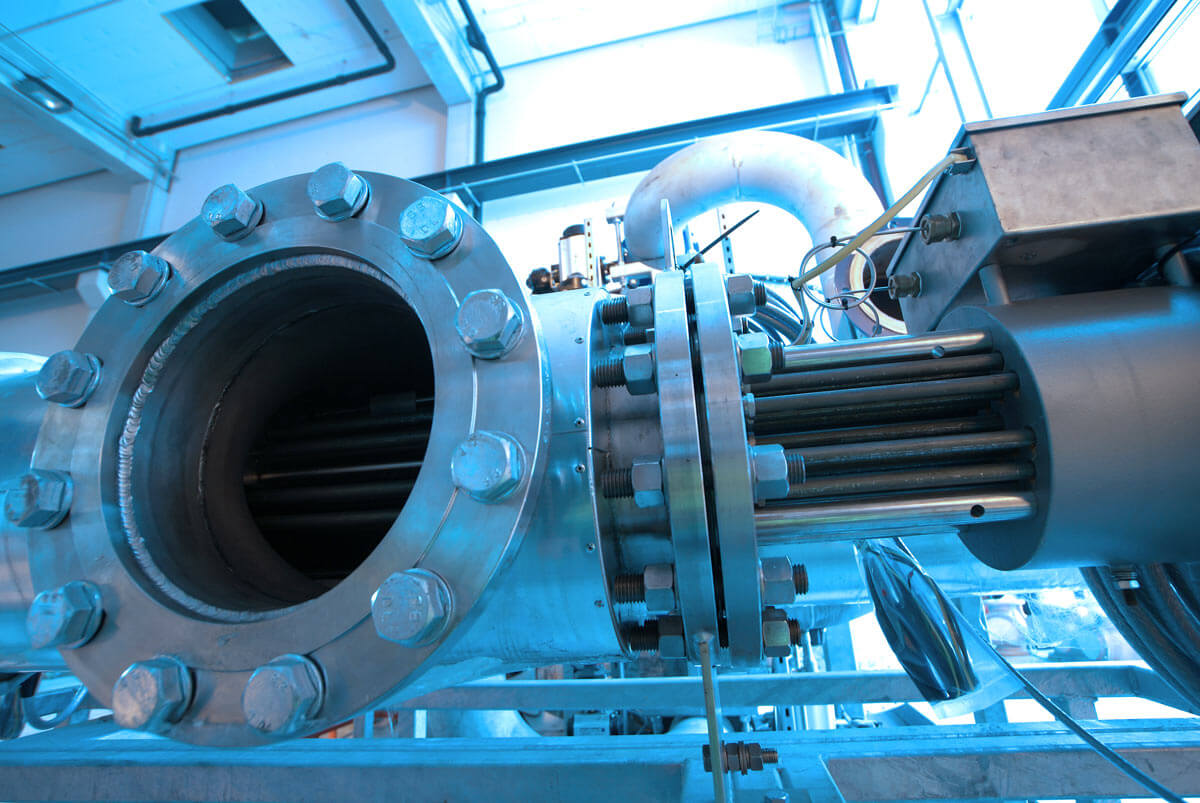
Nuclear
Electropolishing and passivation are both widely used processes in the nuclear industry. Often used for parts that will be subjected to radioactive environments where surface smoothness cleanability is very important.
Learn More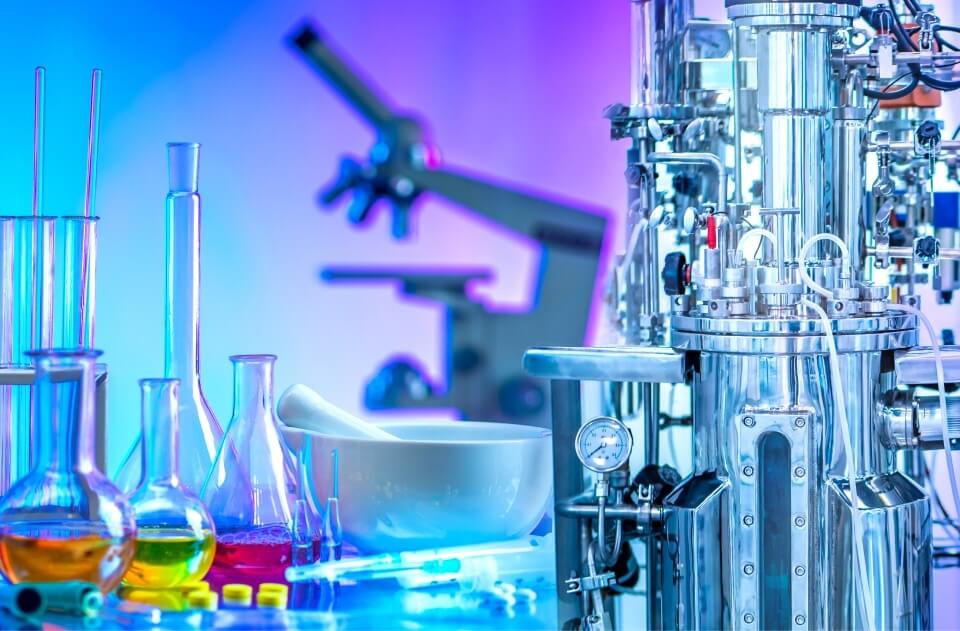
Pharmaceuticals & Bio-Processing
In the high-stakes industries of pharmaceuticals and bio-processing, precision, purity, and product quality are non-negotiable.
Learn MoreDo you have questions?
Ask an expert today.
Give us a call or fill out the form below and one of our team members will be in touch as soon as possible.
*marks required fields
Or Give Us a Call
(847) 683-4100